TRANSITION FLOW
Mixing is a common practice used in a vast majority of industrial processing and manufacturing applications. Mixing is typically studied in either the laminar or turbulent flow regimes because the equations governing these regimes are well understood. Due to the complexity of transition mixing, minimal modeling is done in this regime. Certain industries naturally find themselves operating in and around the transition regime, but are unable to fully understand the process due to the inability of accurate modeling. The mixing of many personal care products fall into this category because they typically deal with complex non-Newtonian fluids. Computational Fluid Dynamics (CFD) is a tool that enables the modeling of various physical systems to analyze velocity profiles, streamlines, and numerous other fluid and flow parameters. Transient simulations of the mixing of Carbopol (a high molecular weight, crosslinked polyacrylic acid polymer) were run using CFD in order to compare the blend time results with real data.
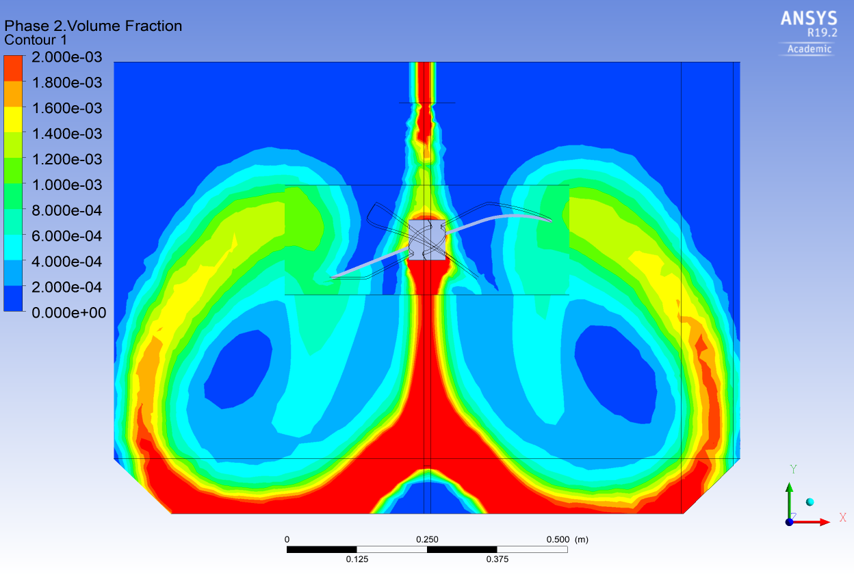
MULTIPHASE IN MIXING
Latex emulsions are systems containing a discrete phase of latex particles dispersed in a continuous aqueous phase and are widely used in industrial mixing processes. In the mixing of latex emulsions, small particles aggregate into larger, more uniform particles to establish a particle size distribution (PSD) required for quality standards. Particle aggregation and colloidal interactions are governed by the Derjaguin, Landau, Verwey, Overbeek (DLVO) theory. Perikinetic aggregation due to Brownian motion is the dominant form of aggregation for very small particles in latex emulsions. Computational Fluid Dynamics (CFD) and Population Balance Modeling (PBM) are two techniques that are used to develop simulations and computational models of the mixing and particle aggregation involved in emulsion mixing processes. CFD is used to model the fluid and flow properties associated with the mixing, whereas PBM uses population balance equations to track the PSD of the latex particles. This project aims to understand the complexities associated with colloidal dispersions and emulsion aggregation in mixing tanks and the issues involved with scaling-up these mixing processes. By examining (1) the velocity profiles, (2) the change of PSD over time, and (3) the specific areas of the tank at which particles accumulate, two tanks of different sizes can be compared. Using ANSYS Fluent, CFD-PBM simulations of latex particle aggregation in water were run in a Pilot Plant tank and a larger Manufacturing tank using a user-defined function (UDF) based in DLVO theory to calculate particle aggregation rates.
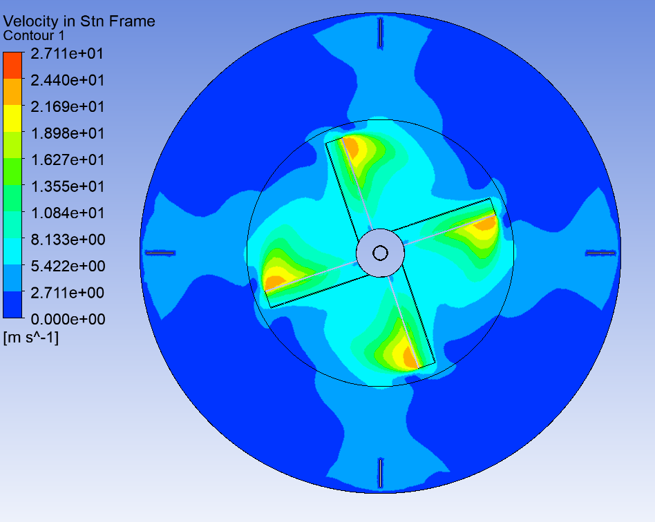