LIQUID METAL BATTERIES
Liquid metal batteries (LMBs) possess the potential to provide a feasible means of grid-scale energy storage for several volatile alternative energy sources, such as solar and wind. These electrochemical cells consist of three unique liquid layers that self-segregate themselves due to differences in both density and miscibility. Specifically, a cell consists of a dense metal cathode, a molten salt electrolyte, and a light metal anode.[1],[2] Moreover, the liquid nature of these layers allow for superior kinetics and transport properties that are not present in other means of energy storage.[1] In this study, the electrolyte layer of a Na|NaOH-NaI|Pb-Bi LMB is investigated with the aid of the computational fluid dynamics (CFD) program ANSYS to analyze fluid flow that is driven by an electro-thermal field within the cell during charge and discharge. Upon creating a computational geometry and a corresponding mesh, ANSYS utilizes finite element analysis (FEA) to simultaneously solve the governing equations of fluid dynamics, heat transfer, and electromagnetism via an iterative process. Through the aid of CFD, insight into the cell’s flow can be obtained that would elsewise be very challenging to obtain via traditional laboratory experiments.
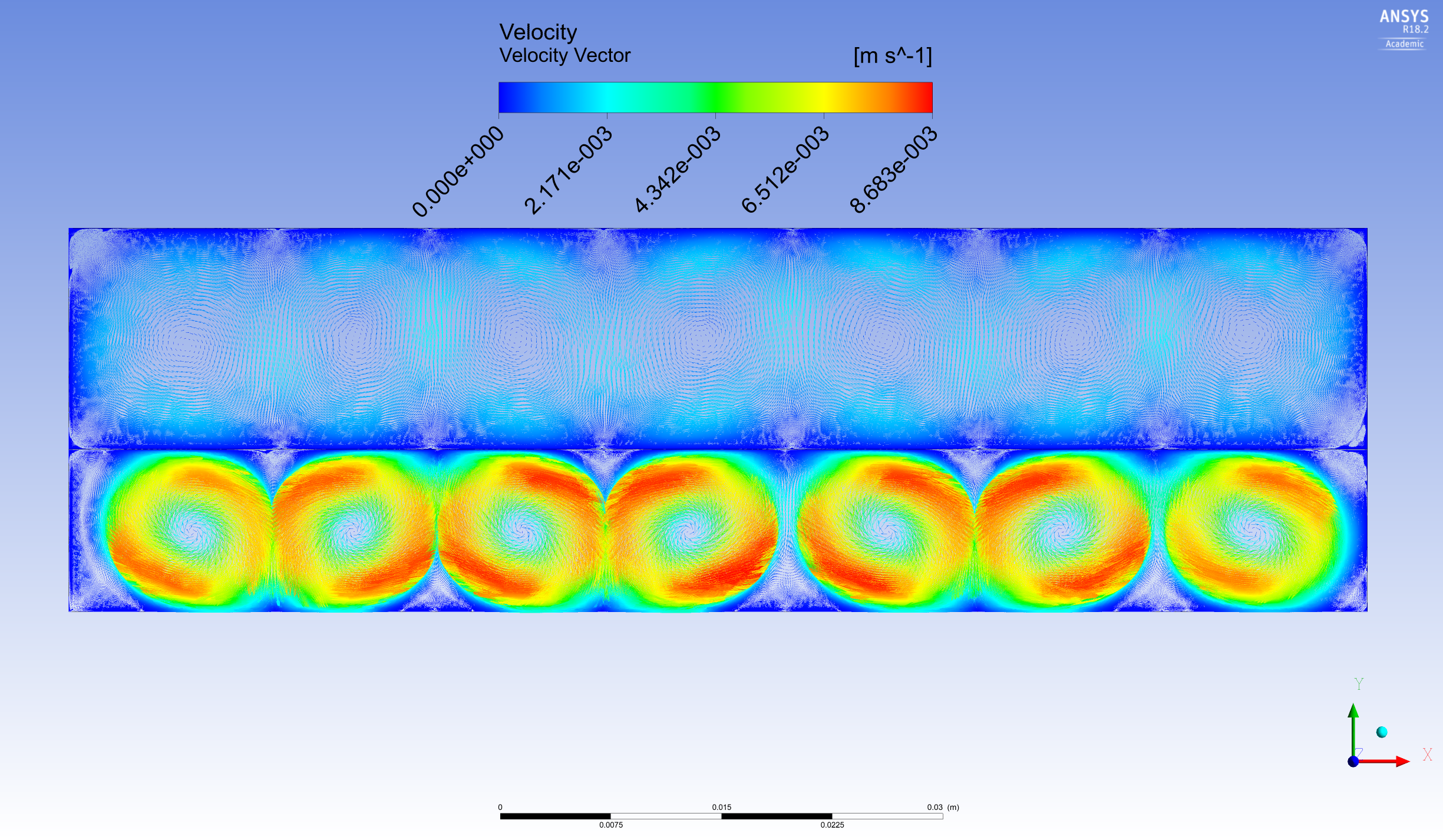
FUEL CELLS
Proton-Exchange Membrane Fuel Cells (PEMFC) are a clean alternative fuel source that harvest energy through the electrochemical conversion of hydrogen and oxygen to water. PEMFCs operate through the oxidation of hydrogen and the reduction of oxygen that are separated by a proton exchange membrane that selectively allows for the transport of hydrogen ions while forcing electrons through the electrical load.[1] The lack of modelling related to the internal properties of a fuel cell has hindered their optimization. Computational Fluid Dynamics (CFD) is a tool that allows for the modelling of many parameters such as species mass fractions, current density, and velocity profiles. Boundary conditions, operating conditions, and material properties for typical PEMFC operation have been identified in the literature[2][3] and will be incorporated into the simulations.
The primary goal moving forward is to expand upon these results to the full serpentine geometry in order to further refine the flow channel parameters. In addition, refinement of the flow channel meshes will lead to the creation of a more accurate simulation for fuel cell geometries.
In addition to this primary goal, this model will be used to test the inclusion of the liquid-phase and joule heating before proceeding to incorporation of the full serpentine model. These optimized simulations will allow for better cell design in order to improve water management by preventing cell flooding.
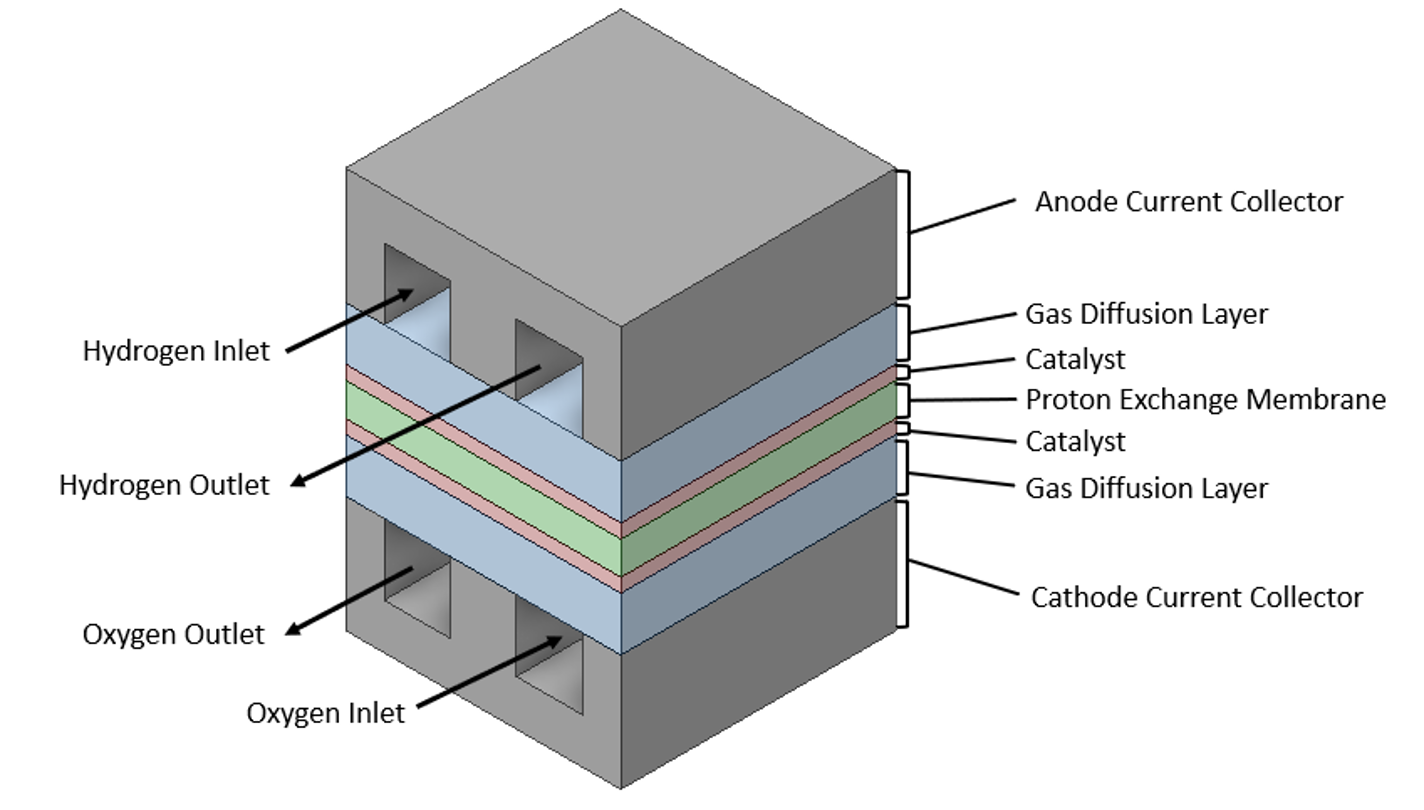